Is Polystyrene Recyclable?
Polystyrene is 100% recyclable with the help of our specialist team, minimising the environmental impact of your polystyrene waste. Over 10,000 tonnes of EPS (Expanded Polystyrene) are recycled each year in the UK, and increasing this rate is our mission.
Due to a lack of local authority services recycling polystyrene, disposing of polystyrene sustainably can be difficult . However, with our professional waste management company, you can ensure this versatile plastic is recycled safely.
EPS Recycling Service
Expanded polystyrene (EPS) is a type of foam that you might commonly know as Styrofoam.
This material is commonly used in the construction industry, for uses such as building insulation in walls, roofs and floors. EPS benefits from an air-filled structure with high impact and water resistance, making it perfect for building materials. The recycling process for polystyrene usually involves sorting, cleaning, shredding, compacting and reprocessing. The recycled polystyrene pellets can then be used as raw material to produce new products.
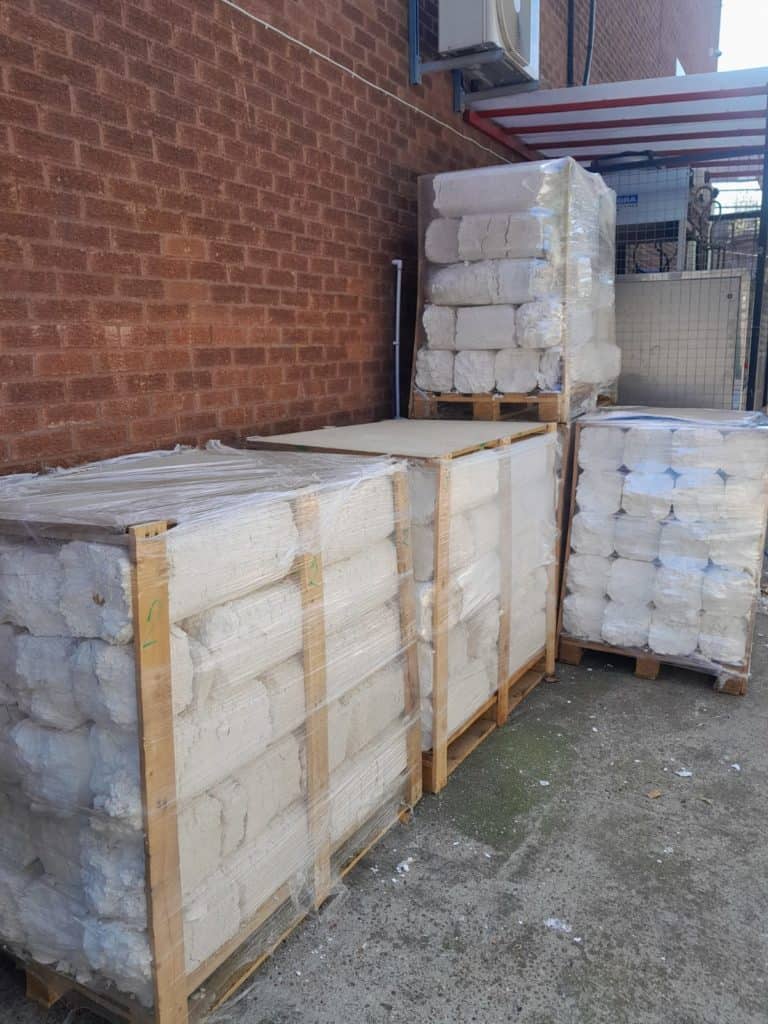